Unmatched Inventory Control And Error-Free Shipment
Our role in your supply chain is to ensure that your product is received accurately, stored and tracked efficiently, and shipped without error. We do this through a combination of facility and equipment, process and procedure, and inventory management systems to tie everything together.
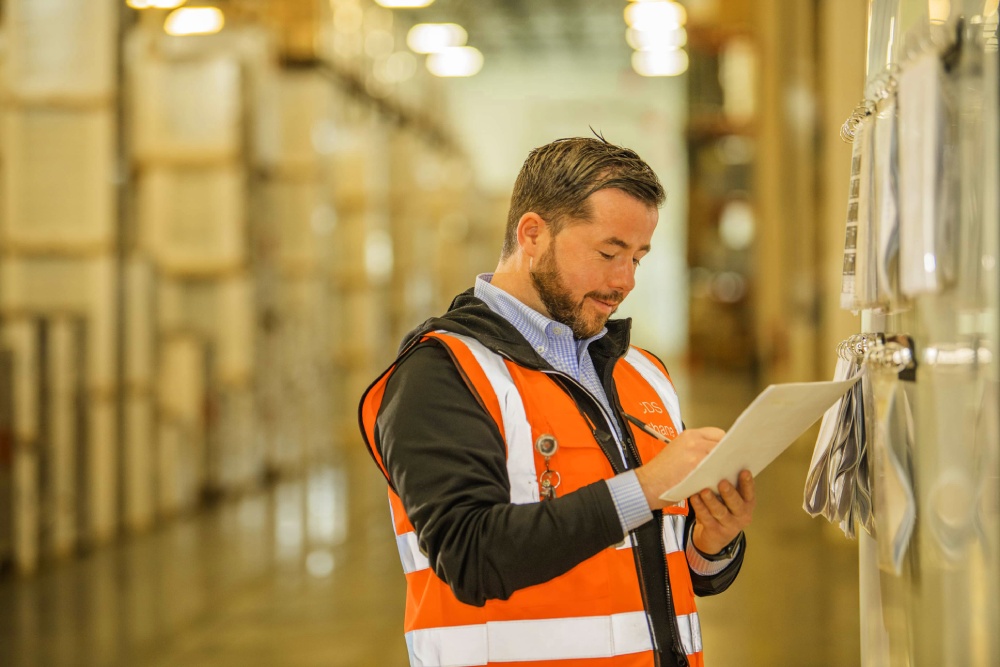
Receiving and Storing Your Products
CDS offers an electronic Advance Ship Notice (ASN), blind receiving with second-level checking, and the ability to use an existing or a CDS-applied pallet ID. The result? You’ll know exactly when new inventory arrives in any of our facilities.
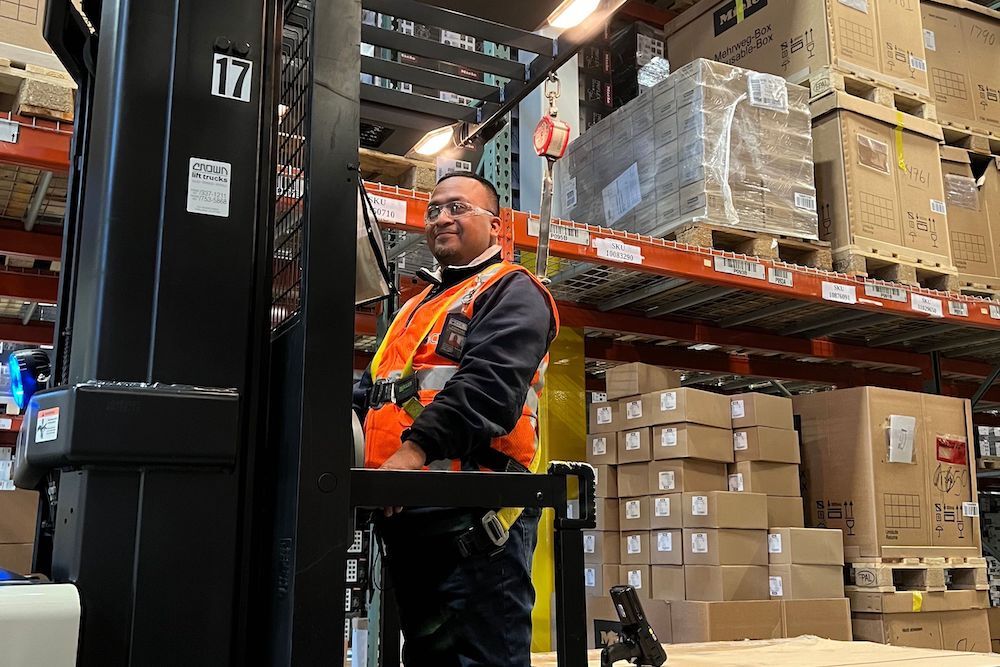
Transparent Inventory Control
CDS facilities are not a black box. When your products are in a CDS facility, you’ll have a clear picture of your inventory. Our user-friendly software interfaces and reports, combined with expert insights from the CDS team, can help improve your organization’s planning and decision-making.
Customizable KPI Reporting via the CDS Web Portal
All of the above processes are backed by customizable KPIs, designed collaboratively with each client to ensure alignment with your specific goals. Reports on these KPIs are sent automatically and are also available through the CDS web portal, providing you with real-time insights and complete transparency. This system allows you to access and analyze your data anytime to monitor performance and make informed decisions.
Product Planning & Characteristics
CDS can handle various product units of measure (pallet, case, each, or specialized), product labeling with 1D or 2D barcode, environmental and hazardous data, and product batch code formats with robust data interpretation and automated hold implementation. This can help you have better insight into the products you have in CDS’s facility, so you can better manage inventory. This is also why CDS is optimized for both B2B and B2C organizations, large or small.
Accurate Order Allocation That Improves Customer Satisfaction
Our services boost customer satisfaction by ensuring accurate, timely deliveries using advanced systems for order processing and inventory management. We prioritize older inventory through FIFO (First-In, First-Out) or FEFO (First-Expired, First-Out), using batch codes and optimized RF allocation to efficiently cycle through stock. Additionally, allocation can be customized by order attributes like scheduled ship times, product lines, or carriers, ensuring precise product distribution based on specific needs.
Efficient & Secure Shipping
At CDS, we work with many different shippers, using various ASN labels and technology integrations to ensure your product gets to the correct end customer. On top of this, our expert warehouse team loads shipments based on product characteristics (such as stack height, weight, and size attributes), to make sure inventory is safe for the entire journey. This leads to happier customers for our clients, and less hassle of dealing with unneeded replacements or returns from damaged shipments.